Activated Sludge Biological Process Plant is perhaps the most challenging treatment system that the operators and the engineers have to deal with and while it will contribute towards the highest COD/BOD reduction, it is also one of the most difficult areas to look after. Managing and handling the operation is not a straight forward approach because, other than having the basic knowledge and understanding of the biochemical process, most of it will rely on close visual observations and test data to maintain a healthy working system. Thus, having something like a handbook that can serve as a troubleshooting guideline will make a whole lot of difference.
The following table will summarize and list down all the common problems faced by typical activated sludge biological treatment system. This will include the possible causes leading to the problem and also the suggestions on how to rectify it. Note that the compilation shown below are mostly based on general observations, including experience and while the corrective actions put forward will work most of the time, there are instances that sometimes it might require more in-depth study and analysis to identify the real root cause behind the issue. At times despite putting forward the remedial actions, it will still not work because wrong assumptions were made and hopefully the troubleshooting guide provided here will help you to make the correct analysis and finally overcome the issue.
The following table will summarize and list down all the common problems faced by typical activated sludge biological treatment system. This will include the possible causes leading to the problem and also the suggestions on how to rectify it. Note that the compilation shown below are mostly based on general observations, including experience and while the corrective actions put forward will work most of the time, there are instances that sometimes it might require more in-depth study and analysis to identify the real root cause behind the issue. At times despite putting forward the remedial actions, it will still not work because wrong assumptions were made and hopefully the troubleshooting guide provided here will help you to make the correct analysis and finally overcome the issue.
Problem | Possible causes | Corrective Actions |
Bulking:Sludge change to very light brown color.Poor settlability of the sludge characterized by high SVI value (>200). This will lead to poor discharge water quality due to the inability of the sludge to properly separate from the water in the clarifier. | a) Insufficient biomass. Usually these can be seen by a sudden drop in MLSS level. The ideal biomass concentration should be between 4000 – 5000ppm depending on the different plant set up and treatment factors such as wastewater characteristics especially on the influent BOD value. b) Growth of filamentous bacteria due to:
| To initiate Bioaugmentation program to introduce and cultivate the right sludge/bacteria type with the desired settling characteristic. Other option such as dosing of binding agents such as polymer to the clarifier can be considered which will help the sludge to form bigger molecules that will settle faster. However, this is only a short-term solution. |
Floating sludge seen in the secondary clarifier Blanket rising and carry over from Sequencing Batch Reactor (SBR) tanks | a) Anoxic condition -Unexpected denitrification happening due to the presence of certain type of bacterial genera. Generally, without a denitrification facility, the nitrate present in the wastewater may denitrify in the aeration basin and the clarifier. b) Sludge is decaying. c) Bulking issue. | a) Control aeration rate to ensure that the best DO level is within 1.5 to 2.0ppm. Avoid over-aeration. b) Increase sludge wasting rate as an approach to lower the sludge age. This is a very subjective approach as there are arguments quoted in certain literature that instead suggest that lower sludge wasting rate will help. If this approach is not workable, then anoxic tank needs to be installed. c) See "Problem on sludge bulking" on ways to deal with the bulking issue caused by filamentous bacteria. |
Deflocculation or pin floc occurrence. This is usually characterized by the presence of very fine particles or tiny pin size solids floating on the surface of the clarifier. Accumulation of these materials can lead to carry over going towards the final discharge causing turbid/cloudy appearance of the effluent. | a) This condition can be due to the sludge characteristic of settling way too fast leaving all the tiny small particles behind b) Low F/M ratio which means that there is too less food for the higher number of microorganisms c) Over aeration or low BOD load d) Insufficient sludge wasting.Presence of toxic substances. | a) Control aeration rate or increase BOD load. b) Increase sludge wasting. c) Eliminate the source of toxic discharge going to the treatment system. |
Decomposition / Sludge decay Mixed liquor very dark brown in color, septic or sourish odor. | a) Low level of dissolved oxygen (anything below 0.3ppm is considered critical) b) Sludge age or sludge retention time is too long in activated sludge basin. | a) Increase duration of aeration phase as long as possible or check the aerator equipment. b) Increase sludge wasting frequency. |
Foaming.There are different types of foam and to identify which type it belongs to will rely solely based on visual inspection. (Refer to the set of pictures below that depicts the type of foams seen in biological system) Foam Type I Whitish in color, thick and frothy. Usually this happens during plant startup when the microorganisms are too young and there is high F/M loading Foam Type II White to light brownish foam. More stable and less frothy. Foam Type III Dark chocolate, stable with thin layer of foam. This is due to aged systems operating on high MLSS concentration Presence of foam can also be due to other factors not biologically related such as presence of detergent in the incoming wastewater. This type of foam tends to be whitish in color, light and fluffy. It will also collapse easily. | For Foam Type I, in a typical plant startup situation, this is usually caused by excessive loading when the MLSS have not reached the optimal value. Wide fluctuations in wastewater characteristics can also lead to this scenario. For Foam Type II, filamentous bacteria is present but not in predominant numbers (can be confirmed by microscopic examination) For Foam Type III, usually you can see presence of rotifer (based on microscopic examination) or worms appearing on the sides of the aeration basin that consume the rotting sludge deposit. This signifies the problem faced by aging system whereby the sludge is too old. Chemical Foaming is caused by presence of detergent due to the incoming influent wastewater characteristics. | For Foam Type I, slow down the loading rate, decrease the wasting rate and wait until the ideal MLSS concentration is reached. For Foam Type II, normally presence of this type of foam is very common and happens in almost every biological treatment system. However, if the condition persists leading to wider surface area of the basin covered in foam, then use the sludge bulking approach to deal with it. For Foam Type III, increase the sludge wasting rate while constantly monitoring the MLSS drop and do a microscopic examination. Check the source and find ways to reduce the detergent from going to the system. Spray antifoam agent / water from a sprinkler system in order to rupture the bubbles in the foam. |
pH decrease - prolonged acidic condition with the pH dropping below 6.0 can inhibit bacterial growth. | a) Nitrification occurs b) Acidic or toxic substances are present. | a) Maintain optimum MLSS concentration by increasing or decreasing the sludge return ratio. Control the aeration rate as well. b) Eliminate source of toxic substances from going to the system. c) Add in diluted caustic solution (10% concentration) through a dosing system. This is the used only as the last approach or for fast remedial action when the pH drops drastically |
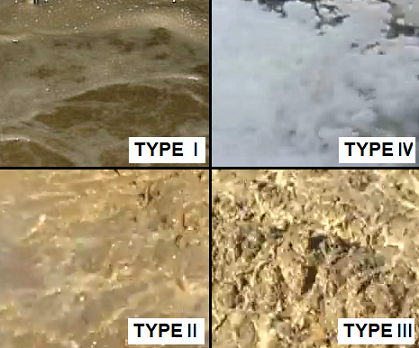
Anticlockwise from top left, type I, II, III and followed by the chemical foam which is white and fluffy.