Belt Filter Press is often applied in wastewater treatment plant sludge dewatering process and it is one of the most cost effective options regardless of the type of sludge feed into the systems. There are several combined processes added into one unit and it involves different applications such as chemical conditioning, gravity drainage and mechanical shearing and compression effect to remove water and dry up the sludge. Today, belt filter presses are widely used and it has become a standard for general wastewater sludge application and thus, learning how to optimize and use it to your advantage is very important.
Chemical conditioning process is the first step that is used to treat the sludge by adding polymer so that it is well-prepared for the later stage. Usually the chemical agent will bind and coagulate the sludge into thicker and easier to handle larger cake size. The conditioned sludge which are now added with chemicals will then be fed into the gravity drainage section whereby this is the most important step that allows the sludge to thicken further. Most of the water is removed during this step and in certain models designed by different manufacturers, some of it will come complete with vacuum utility that allows more water to be drained off compared to conventional unit and during this process it also helps to remove odor as well.
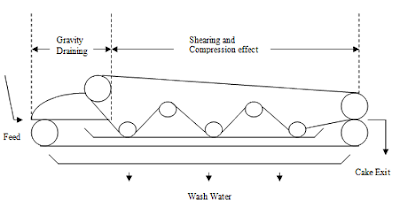
System and operation wise, efficiency of a belt filter press can be further enhanced by adding supporting utilities such as accurate polymer dosing pumps, high capacity sludge feed pumps and high performance conveyor belt system that can last through the shearing effect and stress thus reducing replacement costs. Certain types and models however, did not require installation of conditioning tank and thus chemical dosing pumps just like in a DAF system will play an important role over here. There are different variables that can affect the performance of the whole system. Depending on the incoming sludge characteristics, generally the thicker and more concentrated the feed, this will result in improved cake dryness. Apart from that, the belt size, porosity and width should not be neglected as all these will also play an important role towards enhanced operations.
So far, calculating and determining capacity load on how much sludge a belt filter press can handle is very important and selection of the right unit to match your incoming feed will help to synchronize all processes together. For example, a wastewater treatment plant that produces a certain fixed volume measured in gallons per day with certain percentage of concentrated solids will require determining the number and size of belts (from 0.5 up to 3.0 meter) to generate the expected solid captures.
Other sludge thickening and drying process using heat application.