Wastewater coming from biodiesel manufacturing consists mainly of unreacted oil and fatty acid in emulsion form and is generated during the transesterification process washing step. Depending on how well the system is managed and operated, sometimes carryover of glycerine that end up in the wastewater can be imminent and this usually results from the poor management of the process operation which occurs during separation of glycerine from the biodiesel and overall, this scenario can also pose a huge problem in the treatment stage. Since alkali is used as a catalyst to speed up the reaction process, the characteristics of the biodiesel wastewater is also expected to be very high in pH reaching almost 11 most of the time and thus, this would require pre-treatment step to bring down the pH close to neutral zone before the wastewater can be treated using bacterial biodegradation. Generally, for every metric ton of biodiesel fuel produced, one should allocate at least minimum about 200kg of raw wastewater for bioremediation and because more concerns actually come from huge production facilities especially for large-scale biodiesel plant, an efficient treatment solution has to be developed to deal with the problem.
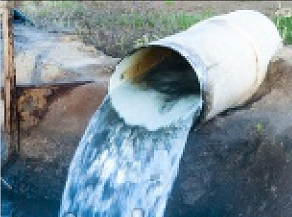
Biological treatment using bacterial biodegradation is actually possible provided that COD load is not at the extreme which might end up disrupting and inhibiting bacterial biochemical activity. Normally with COD load less than 10000 mg/l present in the wastewater, the bacteria should be able to deal with it provided that urea as nitrogen source is provided in a ratio enough to sustain its growth. However, use of this treatment option presents many obstacles and challenges because upset of the whole biological system is very common especially in conditions whereby carryover of methanol, glycerine or soap as the by-product can result in high strength COD wastewater that instead becomes toxic and kills the microorganisms. Furthermore, with the fluctuating hydraulic load rate fed to the system which is commonly seen in biodiesel plant also means that control and adjustment has to be done immediately or else, without a stable working system, things can be very difficult to maintain. Further investigations done by researchers in field studies also examined and concluded there is also a relationship between high solid content (oils and fats) in the wastewater and how it can effect the growth of microorganisms. With that in mind, pre-treatment steps are normally introduced either using flotation principle in order to create floc to float up, then skim off the solid materials with the help of binding agents or electrocoagulation process can also be applied to separate out the solid content from the wastewater.
Anaerobic co-digestion
Another alternative to treat the biodiesel wastewater is to use it as co-digestion feedstock together with the glycerine or any other types of organic waste using the anaerobic digestion process route to generate biogas. Usually the process is carried out in a single-stage digester containing anaerobic sludge which can be obtained from municipal sewage treatment plant. The benefit of using this approach is that anaerobic co-digestion is generally more stable and can be controlled more easily while the methane produced in the reactor can also be utilized for other purpose. Depending on how well the engineer managed the system, biodegradability of the waste can be as high as 95 to 98% with most of the energy generated from COD reduction were consumed to produce methane gas. Methane yield coefficient which is the common term used to measure efficiency of the whole treatment system can vary considerable but a general guideline should be in the range of 250 – 300 of ml methane expected per gram of COD removed. Usually anaerobic co-digestion of glycerine together with the biodiesel wastewater treatment follows a two-step process, whereby the first step which involves pre-treatment will require acidification (using either phosphoric acid or sulphuric acid) in order to recover back the catalyst, then followed by electrocoagulation before the wastewater is fed to the digester.
MBR Technology
Most recently, with MBR (membrane bioreactor) gaining popularity mainly due to the reduction of membrane manufacturing cost and improved quality, research studies have shifted focus towards finding out on whether it can offer a viable treatment option for biodiesel wastewater. The design consideration can be different depending on where the membranes are located but most of it these days involved the submerged type with sections or partitions created acting as pre-treatment stage before the wastewater reaches the membrane. So far, this technology has not been applied full scale in biodiesel plants and its use is mostly limited in small communities and individual households but looking at the progress it has been made over the years, it could possible that with further improvements coupled with new technologies based on membrane systems, it can be adopted to effectively treat the biodiesel wastewater.