Basket Centrifuge is usually used for dewatering wastewater sludge in a slurry form. It is usually operated in a batch wise process and it is typically applied in treatment plants whereby high amount of solid recovery is very important towards getting a clear water discharge. Normally the cakes obtained using this solid/liquid separation technique is very dry and thus its application in wastewater treatment is usually towards the end of the final discharge in which it acts as a polishing stage.
A normal design and buildup of a typical basket centrifuge usually contains either a perforated drum with holes for the water to pass through or one in which the drum has a solid wall surface without any holes (imperforated). The first one, perforated type, sludge medium will enter to the drum and then under centrifugal force, the water will move away towards outside of the drum and it will be collected and drained out. The other one which is imperforated, water can only be separated from the sludge when it overflows from the top of the bowl. Regardless of design, both sludge/water separations can still be achieved although the perforated type provide a slight advantage compared to the other.
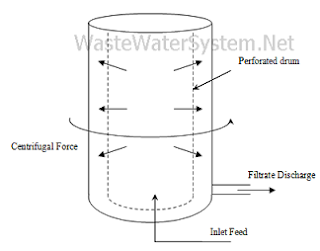
Despite the advantage of achieving higher degree of sludge cake dryness and ease of control in the operation, basket centrifuge will need constant stoppage after every single run. Remember what we mentioned earlier whereby the unit is operating on batch wise process, after every cycle, it will need some time to clear out the cake before the next batch can proceed. Usually high end designs have a built-in wash spray nozzles but on older designs, usually there is a knife or plow to scrape and make the cake drop from the surface. Capacity wise, it might not be able to cope with large wastewater treatment plants but on small scaled industries using small treatment setup, it will definitely offer the best alternative other than using a granular media filter.
Overall, apart from this capacity setback, performance wise, basket centrifuge is most suitable when it comes to getting better cake dryness and clearer wastewater filtrate. Choice of other methods to dewater waste sludge can also be achieved using rotary vacuum filtration.